Quality Assurance Manager
Posted on Oct 9, 2024 by Dynamic Ratings, Inc.
Sussex, WI
Other
Immediate Start
Annual Salary
Full-Time
Dynamic Ratings continues to grow and we are adding to our management team! The Quality Assurance Manager is responsible for overseeing and ensuring the highest standards of process and product quality within our company.
In this role, your primary responsibilities include:
Integrated Management System (IMS) Administration: Develop, implement, and maintain the company’s Integrated Management System in compliance with industry standards and regulatory requirements. Ensure that all processes are documented, standardized, and consistently followed.
Product Quality: Oversee all aspects of product quality, from raw materials through to finished goods. Ensure that products meet or exceed customer specifications and regulatory requirements.
Process Quality: Monitor and evaluate production processes to ensure consistency and compliance with established standards. Identify areas for process improvement and work with cross-functional teams to implement solutions.
Auditing and Compliance: Conduct regular internal audits of processes and products to ensure compliance with QMS, industry standards, and customer requirements. Lead external audits and ensure successful certification and recertification.
Continuous Improvement: Lead continuous improvement initiatives focused on enhancing product quality, process efficiency, and customer satisfaction. Utilize quality tools and methodologies (e.g., Six Sigma, Lean) to identify and eliminate waste, reduce variability, and improve overall quality.
Root Cause Analysis: Investigate and analyze quality issues, non-conformances, and customer complaints. Perform root cause analysis and implement corrective and preventive actions to resolve issues and prevent recurrence.
Supplier Quality Management: Collaborate with the procurement team to evaluate and qualify suppliers, ensuring that all incoming materials meet the company’s quality standards. Conduct supplier audits and work with suppliers to resolve quality issues.
Training and Development: Provide training and support to staff on quality standards, procedures, and best practices. Foster a culture of quality awareness and continuous improvement throughout the organization.
Reporting and Documentation: Prepare and present reports on quality performance, audit results, non-conformances, and improvement initiatives to senior management. Maintain accurate and up-to-date documentation related to quality processes and products.
Requirements
The right person for this role will be a detail-oriented problem solver with strong analytical skills. You should be knowledgeable in quality management systems, industry standards, and regulatory requirements; and be proficient in quality tools and methodologies (e.g., Six Sigma, Lean, Root Cause Analysis). Strong leadership and team management skills are crucial to be successful in this role, along with excellent communication, interpersonal, and organizational skills.
Additionally, you should possess a bachelor’s degree in Quality Assurance, Engineering, or a related field and have at least 5 years of experience in a quality assurance role within a manufacturing environment; or an equivalent combination of education and experience. Certified Quality Manager (CQM) or Six Sigma Black Belt is a plus.
Benefits
Competitive pay
Comprehensive health, dental, and vision insurance
Disability benefits
401(k) retirement plan with company match
Paid time off
Opportunities for professional development and advancement
In this role, your primary responsibilities include:
Integrated Management System (IMS) Administration: Develop, implement, and maintain the company’s Integrated Management System in compliance with industry standards and regulatory requirements. Ensure that all processes are documented, standardized, and consistently followed.
Product Quality: Oversee all aspects of product quality, from raw materials through to finished goods. Ensure that products meet or exceed customer specifications and regulatory requirements.
Process Quality: Monitor and evaluate production processes to ensure consistency and compliance with established standards. Identify areas for process improvement and work with cross-functional teams to implement solutions.
Auditing and Compliance: Conduct regular internal audits of processes and products to ensure compliance with QMS, industry standards, and customer requirements. Lead external audits and ensure successful certification and recertification.
Continuous Improvement: Lead continuous improvement initiatives focused on enhancing product quality, process efficiency, and customer satisfaction. Utilize quality tools and methodologies (e.g., Six Sigma, Lean) to identify and eliminate waste, reduce variability, and improve overall quality.
Root Cause Analysis: Investigate and analyze quality issues, non-conformances, and customer complaints. Perform root cause analysis and implement corrective and preventive actions to resolve issues and prevent recurrence.
Supplier Quality Management: Collaborate with the procurement team to evaluate and qualify suppliers, ensuring that all incoming materials meet the company’s quality standards. Conduct supplier audits and work with suppliers to resolve quality issues.
Training and Development: Provide training and support to staff on quality standards, procedures, and best practices. Foster a culture of quality awareness and continuous improvement throughout the organization.
Reporting and Documentation: Prepare and present reports on quality performance, audit results, non-conformances, and improvement initiatives to senior management. Maintain accurate and up-to-date documentation related to quality processes and products.
Requirements
The right person for this role will be a detail-oriented problem solver with strong analytical skills. You should be knowledgeable in quality management systems, industry standards, and regulatory requirements; and be proficient in quality tools and methodologies (e.g., Six Sigma, Lean, Root Cause Analysis). Strong leadership and team management skills are crucial to be successful in this role, along with excellent communication, interpersonal, and organizational skills.
Additionally, you should possess a bachelor’s degree in Quality Assurance, Engineering, or a related field and have at least 5 years of experience in a quality assurance role within a manufacturing environment; or an equivalent combination of education and experience. Certified Quality Manager (CQM) or Six Sigma Black Belt is a plus.
Benefits
Competitive pay
Comprehensive health, dental, and vision insurance
Disability benefits
401(k) retirement plan with company match
Paid time off
Opportunities for professional development and advancement
Reference: 203845500
https://jobs.careeraddict.com/post/96045547
Quality Assurance Manager
Posted on Oct 9, 2024 by Dynamic Ratings, Inc.
Sussex, WI
Other
Immediate Start
Annual Salary
Full-Time
Dynamic Ratings continues to grow and we are adding to our management team! The Quality Assurance Manager is responsible for overseeing and ensuring the highest standards of process and product quality within our company.
In this role, your primary responsibilities include:
Integrated Management System (IMS) Administration: Develop, implement, and maintain the company’s Integrated Management System in compliance with industry standards and regulatory requirements. Ensure that all processes are documented, standardized, and consistently followed.
Product Quality: Oversee all aspects of product quality, from raw materials through to finished goods. Ensure that products meet or exceed customer specifications and regulatory requirements.
Process Quality: Monitor and evaluate production processes to ensure consistency and compliance with established standards. Identify areas for process improvement and work with cross-functional teams to implement solutions.
Auditing and Compliance: Conduct regular internal audits of processes and products to ensure compliance with QMS, industry standards, and customer requirements. Lead external audits and ensure successful certification and recertification.
Continuous Improvement: Lead continuous improvement initiatives focused on enhancing product quality, process efficiency, and customer satisfaction. Utilize quality tools and methodologies (e.g., Six Sigma, Lean) to identify and eliminate waste, reduce variability, and improve overall quality.
Root Cause Analysis: Investigate and analyze quality issues, non-conformances, and customer complaints. Perform root cause analysis and implement corrective and preventive actions to resolve issues and prevent recurrence.
Supplier Quality Management: Collaborate with the procurement team to evaluate and qualify suppliers, ensuring that all incoming materials meet the company’s quality standards. Conduct supplier audits and work with suppliers to resolve quality issues.
Training and Development: Provide training and support to staff on quality standards, procedures, and best practices. Foster a culture of quality awareness and continuous improvement throughout the organization.
Reporting and Documentation: Prepare and present reports on quality performance, audit results, non-conformances, and improvement initiatives to senior management. Maintain accurate and up-to-date documentation related to quality processes and products.
Requirements
The right person for this role will be a detail-oriented problem solver with strong analytical skills. You should be knowledgeable in quality management systems, industry standards, and regulatory requirements; and be proficient in quality tools and methodologies (e.g., Six Sigma, Lean, Root Cause Analysis). Strong leadership and team management skills are crucial to be successful in this role, along with excellent communication, interpersonal, and organizational skills.
Additionally, you should possess a bachelor’s degree in Quality Assurance, Engineering, or a related field and have at least 5 years of experience in a quality assurance role within a manufacturing environment; or an equivalent combination of education and experience. Certified Quality Manager (CQM) or Six Sigma Black Belt is a plus.
Benefits
Competitive pay
Comprehensive health, dental, and vision insurance
Disability benefits
401(k) retirement plan with company match
Paid time off
Opportunities for professional development and advancement
In this role, your primary responsibilities include:
Integrated Management System (IMS) Administration: Develop, implement, and maintain the company’s Integrated Management System in compliance with industry standards and regulatory requirements. Ensure that all processes are documented, standardized, and consistently followed.
Product Quality: Oversee all aspects of product quality, from raw materials through to finished goods. Ensure that products meet or exceed customer specifications and regulatory requirements.
Process Quality: Monitor and evaluate production processes to ensure consistency and compliance with established standards. Identify areas for process improvement and work with cross-functional teams to implement solutions.
Auditing and Compliance: Conduct regular internal audits of processes and products to ensure compliance with QMS, industry standards, and customer requirements. Lead external audits and ensure successful certification and recertification.
Continuous Improvement: Lead continuous improvement initiatives focused on enhancing product quality, process efficiency, and customer satisfaction. Utilize quality tools and methodologies (e.g., Six Sigma, Lean) to identify and eliminate waste, reduce variability, and improve overall quality.
Root Cause Analysis: Investigate and analyze quality issues, non-conformances, and customer complaints. Perform root cause analysis and implement corrective and preventive actions to resolve issues and prevent recurrence.
Supplier Quality Management: Collaborate with the procurement team to evaluate and qualify suppliers, ensuring that all incoming materials meet the company’s quality standards. Conduct supplier audits and work with suppliers to resolve quality issues.
Training and Development: Provide training and support to staff on quality standards, procedures, and best practices. Foster a culture of quality awareness and continuous improvement throughout the organization.
Reporting and Documentation: Prepare and present reports on quality performance, audit results, non-conformances, and improvement initiatives to senior management. Maintain accurate and up-to-date documentation related to quality processes and products.
Requirements
The right person for this role will be a detail-oriented problem solver with strong analytical skills. You should be knowledgeable in quality management systems, industry standards, and regulatory requirements; and be proficient in quality tools and methodologies (e.g., Six Sigma, Lean, Root Cause Analysis). Strong leadership and team management skills are crucial to be successful in this role, along with excellent communication, interpersonal, and organizational skills.
Additionally, you should possess a bachelor’s degree in Quality Assurance, Engineering, or a related field and have at least 5 years of experience in a quality assurance role within a manufacturing environment; or an equivalent combination of education and experience. Certified Quality Manager (CQM) or Six Sigma Black Belt is a plus.
Benefits
Competitive pay
Comprehensive health, dental, and vision insurance
Disability benefits
401(k) retirement plan with company match
Paid time off
Opportunities for professional development and advancement
Reference: 203845500
Share this job:
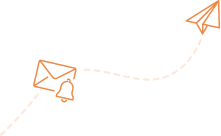
Alert me to jobs like this:
Amplify your job search:
Expert career advice
Increase interview chances with our downloads and specialist services.
Visit Blog