Production Supervisor
Posted on Sep 28, 2024 by Yokohama Tire Corporation
West Point, MS
Manufacturing
Immediate Start
Annual Salary
Full-Time
Summary:
Supervise activities of division employees to assure that production activities are completed to meet quality, safety and productivity standards.
Responsibilities:
• Prepares and execute plans based on production schedule optimizing man and machine’s productivity with minimal scrap and defects. • Monitors and confirms conditions of all safety devices by routine and through safety check sheets to ensure safety of the working environment and takes immediate countermeasure for any unsafe acts and conditions. • Checks regularly and confirms that all machine settings and set-up are correct and updated. • Monitors and checks operator’s compliance on standard operating procedures (SOP), FMEA, Process Flow, Control Plan and other related standards in performing their assigned jobs. • Initiate and facilitate countermeasures for immediate recovery from any downtime (machine, quality, material shortage, etc.). • Conducts lot flow analysis through factual investigation to account all affected lots in case of non-conformities (process and product) and finally hold all affected lots. • Monitor proper handling and usage of machine and equipment, tools and support materials, factory supplies and other utilities to maximize useful life. • Leads improvement activities related to SEQDC including 5S using tools such as Quality Circles, TPM, small group activities and the like. • Assist the Trainer in conducting on-the-job training (OJT) to his subordinates to upgrade competencies and become multi-skilled workers. • Prepares shift’s accomplishment report and ensure proper turnover of work for the next shift. • Implements good housekeeping using 5S tools. • Motivates and uplift the morale of subordinates. • Promotes safety and quality awareness and consciousness within the group • Promotes good working relationship among the group and to other groups as well • Monitor and control overtime work • Operates machines and equipment during emergency situations • Performs other duties as required (meetings, reports, etc.)
Knowledge and Skills:
• Heavy Equipment Operation • Minor Troubleshooting • Conducting On-the-Job Training • Leadership and Human Resource Management • Data Analysis and Interpretation • Oral and Written Communications Including Technical Writing Using MS Office Software such as Word, Excel and Power Point • Presentation skills
Education and Experience:
• Must have 5 + years as a first line supervisor or manager.
Physical Requirements:
• Occasional (1-33%) material handling that consists of pulling, pushing, carrying, lifting above shoulder, lifting waist to shoulder, lifting floor to waist. • Occasional (1-33%) non material handling that consists of sitting, standing, walking, bending, reaching, climbing, crawling, squatting, kneeling, and twisting. • Occasional (1-33%) floor to waist lifting over 70 pounds. • Occasional (1-33%) waist to shoulder lifting of over 70 pounds. • Occasional (1-33%) lifting above the shoulder over 70 pounds • Use of both hands for simple grasping, pushing and pulling • All lifting activities cover both lifting and lowering processes. The point of origin and/or the destination of the lift are classified in the three body zone ranges
Supervise activities of division employees to assure that production activities are completed to meet quality, safety and productivity standards.
Responsibilities:
• Prepares and execute plans based on production schedule optimizing man and machine’s productivity with minimal scrap and defects. • Monitors and confirms conditions of all safety devices by routine and through safety check sheets to ensure safety of the working environment and takes immediate countermeasure for any unsafe acts and conditions. • Checks regularly and confirms that all machine settings and set-up are correct and updated. • Monitors and checks operator’s compliance on standard operating procedures (SOP), FMEA, Process Flow, Control Plan and other related standards in performing their assigned jobs. • Initiate and facilitate countermeasures for immediate recovery from any downtime (machine, quality, material shortage, etc.). • Conducts lot flow analysis through factual investigation to account all affected lots in case of non-conformities (process and product) and finally hold all affected lots. • Monitor proper handling and usage of machine and equipment, tools and support materials, factory supplies and other utilities to maximize useful life. • Leads improvement activities related to SEQDC including 5S using tools such as Quality Circles, TPM, small group activities and the like. • Assist the Trainer in conducting on-the-job training (OJT) to his subordinates to upgrade competencies and become multi-skilled workers. • Prepares shift’s accomplishment report and ensure proper turnover of work for the next shift. • Implements good housekeeping using 5S tools. • Motivates and uplift the morale of subordinates. • Promotes safety and quality awareness and consciousness within the group • Promotes good working relationship among the group and to other groups as well • Monitor and control overtime work • Operates machines and equipment during emergency situations • Performs other duties as required (meetings, reports, etc.)
Knowledge and Skills:
• Heavy Equipment Operation • Minor Troubleshooting • Conducting On-the-Job Training • Leadership and Human Resource Management • Data Analysis and Interpretation • Oral and Written Communications Including Technical Writing Using MS Office Software such as Word, Excel and Power Point • Presentation skills
Education and Experience:
• Must have 5 + years as a first line supervisor or manager.
Physical Requirements:
• Occasional (1-33%) material handling that consists of pulling, pushing, carrying, lifting above shoulder, lifting waist to shoulder, lifting floor to waist. • Occasional (1-33%) non material handling that consists of sitting, standing, walking, bending, reaching, climbing, crawling, squatting, kneeling, and twisting. • Occasional (1-33%) floor to waist lifting over 70 pounds. • Occasional (1-33%) waist to shoulder lifting of over 70 pounds. • Occasional (1-33%) lifting above the shoulder over 70 pounds • Use of both hands for simple grasping, pushing and pulling • All lifting activities cover both lifting and lowering processes. The point of origin and/or the destination of the lift are classified in the three body zone ranges
Reference: 202649551
https://jobs.careeraddict.com/post/95644768
Production Supervisor
Posted on Sep 28, 2024 by Yokohama Tire Corporation
West Point, MS
Manufacturing
Immediate Start
Annual Salary
Full-Time
Summary:
Supervise activities of division employees to assure that production activities are completed to meet quality, safety and productivity standards.
Responsibilities:
• Prepares and execute plans based on production schedule optimizing man and machine’s productivity with minimal scrap and defects. • Monitors and confirms conditions of all safety devices by routine and through safety check sheets to ensure safety of the working environment and takes immediate countermeasure for any unsafe acts and conditions. • Checks regularly and confirms that all machine settings and set-up are correct and updated. • Monitors and checks operator’s compliance on standard operating procedures (SOP), FMEA, Process Flow, Control Plan and other related standards in performing their assigned jobs. • Initiate and facilitate countermeasures for immediate recovery from any downtime (machine, quality, material shortage, etc.). • Conducts lot flow analysis through factual investigation to account all affected lots in case of non-conformities (process and product) and finally hold all affected lots. • Monitor proper handling and usage of machine and equipment, tools and support materials, factory supplies and other utilities to maximize useful life. • Leads improvement activities related to SEQDC including 5S using tools such as Quality Circles, TPM, small group activities and the like. • Assist the Trainer in conducting on-the-job training (OJT) to his subordinates to upgrade competencies and become multi-skilled workers. • Prepares shift’s accomplishment report and ensure proper turnover of work for the next shift. • Implements good housekeeping using 5S tools. • Motivates and uplift the morale of subordinates. • Promotes safety and quality awareness and consciousness within the group • Promotes good working relationship among the group and to other groups as well • Monitor and control overtime work • Operates machines and equipment during emergency situations • Performs other duties as required (meetings, reports, etc.)
Knowledge and Skills:
• Heavy Equipment Operation • Minor Troubleshooting • Conducting On-the-Job Training • Leadership and Human Resource Management • Data Analysis and Interpretation • Oral and Written Communications Including Technical Writing Using MS Office Software such as Word, Excel and Power Point • Presentation skills
Education and Experience:
• Must have 5 + years as a first line supervisor or manager.
Physical Requirements:
• Occasional (1-33%) material handling that consists of pulling, pushing, carrying, lifting above shoulder, lifting waist to shoulder, lifting floor to waist. • Occasional (1-33%) non material handling that consists of sitting, standing, walking, bending, reaching, climbing, crawling, squatting, kneeling, and twisting. • Occasional (1-33%) floor to waist lifting over 70 pounds. • Occasional (1-33%) waist to shoulder lifting of over 70 pounds. • Occasional (1-33%) lifting above the shoulder over 70 pounds • Use of both hands for simple grasping, pushing and pulling • All lifting activities cover both lifting and lowering processes. The point of origin and/or the destination of the lift are classified in the three body zone ranges
Supervise activities of division employees to assure that production activities are completed to meet quality, safety and productivity standards.
Responsibilities:
• Prepares and execute plans based on production schedule optimizing man and machine’s productivity with minimal scrap and defects. • Monitors and confirms conditions of all safety devices by routine and through safety check sheets to ensure safety of the working environment and takes immediate countermeasure for any unsafe acts and conditions. • Checks regularly and confirms that all machine settings and set-up are correct and updated. • Monitors and checks operator’s compliance on standard operating procedures (SOP), FMEA, Process Flow, Control Plan and other related standards in performing their assigned jobs. • Initiate and facilitate countermeasures for immediate recovery from any downtime (machine, quality, material shortage, etc.). • Conducts lot flow analysis through factual investigation to account all affected lots in case of non-conformities (process and product) and finally hold all affected lots. • Monitor proper handling and usage of machine and equipment, tools and support materials, factory supplies and other utilities to maximize useful life. • Leads improvement activities related to SEQDC including 5S using tools such as Quality Circles, TPM, small group activities and the like. • Assist the Trainer in conducting on-the-job training (OJT) to his subordinates to upgrade competencies and become multi-skilled workers. • Prepares shift’s accomplishment report and ensure proper turnover of work for the next shift. • Implements good housekeeping using 5S tools. • Motivates and uplift the morale of subordinates. • Promotes safety and quality awareness and consciousness within the group • Promotes good working relationship among the group and to other groups as well • Monitor and control overtime work • Operates machines and equipment during emergency situations • Performs other duties as required (meetings, reports, etc.)
Knowledge and Skills:
• Heavy Equipment Operation • Minor Troubleshooting • Conducting On-the-Job Training • Leadership and Human Resource Management • Data Analysis and Interpretation • Oral and Written Communications Including Technical Writing Using MS Office Software such as Word, Excel and Power Point • Presentation skills
Education and Experience:
• Must have 5 + years as a first line supervisor or manager.
Physical Requirements:
• Occasional (1-33%) material handling that consists of pulling, pushing, carrying, lifting above shoulder, lifting waist to shoulder, lifting floor to waist. • Occasional (1-33%) non material handling that consists of sitting, standing, walking, bending, reaching, climbing, crawling, squatting, kneeling, and twisting. • Occasional (1-33%) floor to waist lifting over 70 pounds. • Occasional (1-33%) waist to shoulder lifting of over 70 pounds. • Occasional (1-33%) lifting above the shoulder over 70 pounds • Use of both hands for simple grasping, pushing and pulling • All lifting activities cover both lifting and lowering processes. The point of origin and/or the destination of the lift are classified in the three body zone ranges
Reference: 202649551
Share this job:
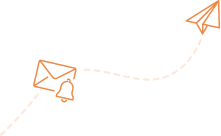
Alert me to jobs like this:
Amplify your job search:
Expert career advice
Increase interview chances with our downloads and specialist services.
Visit Blog