Lead Operator - Prod Ops (Second Shift)
Posted on Oct 7, 2024 by Cordis
Santa Clara, CA
Other
Immediate Start
Annual Salary
Full-Time
Overview:
About Us:
Cordis is an independent, customer-focused global provider of interventional cardiovascular medical technologies. During our 60+ year history we’ve established a legacy of pioneering breakthrough technologies, including the first guiding catheters and coronary drug eluting stents. Cordis has built a strong global footprint that spans over 70 countries.
We’re teammates, not just employees. Our culture empowers you to act like an owner and unleash your full potential in the process. With diverse teams on a global scale, we foster an inclusive atmosphere where everyone is embraced for who they are, their unique perspective, and what they bring to the table. We believe the richness of our experiences and backgrounds enhances the careers of our teammates, the service to our customers, and ultimately, the lives of our patients.
If you love a challenge and are ready to have a direct, positive impact on the lives of millions, then Cordis is just the place for you. Join us, and let’s improve the wellbeing of millions, together.
We are the people behind the people who keep saving lives.
The 2nd shift Lead Operator, Production Ops builds product by following all Quality Systems and Processes (in which trained and certified to) and complete other assigned tasks while meeting manufacturing goals and metrics.
Responsibilities:
Adheres to all Quality Policies and Systems of the Company.
Maintains accurate records, including Lot History Records (LHR), and adheres to all GMP/GDP Policies.
Must be able to manage 20+ team members in work area.
Must be able to create work schedules based on production build schedule.
Must be able to process small parts under a microscope.
Frequently exceeds the average cycle time and quality standard requirements for the stations/processes trained/certified to.
Maintains an good level of attendance (including scheduled overtime)
Trains and possesses a detailed understanding of all processes in their area of responsibility.
Responsible and accountable to train teammates or other manufacturing support (I.e., MEs, QA, R&D, and ect.)
Flexes and rotates to other stations as necessary or assigned.
Maintains a professional work relationship with other team members and other cross‐functional groups.
Proficient in a wide variety of operations; can function as a subject matter expert (SME) for the area to help train and/or identify process improvements.
Helps to ensure that the teams are consistently maintaining accurate records.
Serves as a role model for ensuring Quality System Regulations adherence.
Analyses production metrics to suggest improvements for inefficiencies on the production floor and maximizes production output while ensuring high product quality.
Understands and follows safety policies and practices, and escalates any issues related to product, Quality or workplace safety.
Follows and adheres to 5S principles and goals.
Effectively fills in for the supervisor when not available; in this role, responsible training others, managing the production floor activities as needed, performing LHR reviews, performing limited troubleshooting activities, and notifying engineering/maintenance of issues.
Coordinates all Engineering Build Request (EBR) and Rework activities (training, execution of EBR, and documentation review. Provide feedback during validation and verification builds.
Encourages team to meet desired production metrics/goals while maintaining quality standards.
Advises the team with limited direction from the production supervisor.
Works with Engineering to develop new processes, provides feedback for the creation of new documentation (i.e. MPI, SOP), and trains others to these documents (as needed)
Consistently identifies improvements opportunities for tooling/fixtures.
Recommends and initiates actions to prevent the occurrence of product non-conformity and assists in the implementation and verification of solutions.
Must have good verbal and written communication skills.
Must be able to work with clear communication with cross functional teams and Engineers.
Demonstrates the ability to communicate with others via emails, written correspondence, ect.
Must have the ability to develop and encourage group communication and process improvement meetings. Facilitates with the implementation of process improvement (Kaizen) and Lean manufacturing activities. Provides feedback or ideas on process improvement i.e., bottleneck areas observed.
Has good understanding of Lean and 5s principles. Help enforce, follows, and adheres to the standards. Help lead groups in performing 5s audits.
Qualifications:
High school diploma or equivalent and 4+ years’ experience in the medical device/pharmaceutical field or in a related area
Must be able to work in a Controlled Environment
Must have good hand‐eye coordination.
Must have a good verbal and written communication skills.
Must be able to work with and clearly communicate with cross functional teams and engineers.
Demonstrates reading, writing and math skills comprehension.
Must be detail oriented and demonstrate a high level of inventory control skills (with respect to accuracy and counts)
Must be able to accurately verify others’ work for accuracy (i.e. work content, actual part counts, LHR documentation)
Must be able to work cross-functional groups to resolve any discrepancies/documentation errors.
Must have intermediate to advanced computer skills (i.e. Microsoft Excel, Word, Outlook)
About Us:
Cordis is an independent, customer-focused global provider of interventional cardiovascular medical technologies. During our 60+ year history we’ve established a legacy of pioneering breakthrough technologies, including the first guiding catheters and coronary drug eluting stents. Cordis has built a strong global footprint that spans over 70 countries.
We’re teammates, not just employees. Our culture empowers you to act like an owner and unleash your full potential in the process. With diverse teams on a global scale, we foster an inclusive atmosphere where everyone is embraced for who they are, their unique perspective, and what they bring to the table. We believe the richness of our experiences and backgrounds enhances the careers of our teammates, the service to our customers, and ultimately, the lives of our patients.
If you love a challenge and are ready to have a direct, positive impact on the lives of millions, then Cordis is just the place for you. Join us, and let’s improve the wellbeing of millions, together.
We are the people behind the people who keep saving lives.
The 2nd shift Lead Operator, Production Ops builds product by following all Quality Systems and Processes (in which trained and certified to) and complete other assigned tasks while meeting manufacturing goals and metrics.
Responsibilities:
Adheres to all Quality Policies and Systems of the Company.
Maintains accurate records, including Lot History Records (LHR), and adheres to all GMP/GDP Policies.
Must be able to manage 20+ team members in work area.
Must be able to create work schedules based on production build schedule.
Must be able to process small parts under a microscope.
Frequently exceeds the average cycle time and quality standard requirements for the stations/processes trained/certified to.
Maintains an good level of attendance (including scheduled overtime)
Trains and possesses a detailed understanding of all processes in their area of responsibility.
Responsible and accountable to train teammates or other manufacturing support (I.e., MEs, QA, R&D, and ect.)
Flexes and rotates to other stations as necessary or assigned.
Maintains a professional work relationship with other team members and other cross‐functional groups.
Proficient in a wide variety of operations; can function as a subject matter expert (SME) for the area to help train and/or identify process improvements.
Helps to ensure that the teams are consistently maintaining accurate records.
Serves as a role model for ensuring Quality System Regulations adherence.
Analyses production metrics to suggest improvements for inefficiencies on the production floor and maximizes production output while ensuring high product quality.
Understands and follows safety policies and practices, and escalates any issues related to product, Quality or workplace safety.
Follows and adheres to 5S principles and goals.
Effectively fills in for the supervisor when not available; in this role, responsible training others, managing the production floor activities as needed, performing LHR reviews, performing limited troubleshooting activities, and notifying engineering/maintenance of issues.
Coordinates all Engineering Build Request (EBR) and Rework activities (training, execution of EBR, and documentation review. Provide feedback during validation and verification builds.
Encourages team to meet desired production metrics/goals while maintaining quality standards.
Advises the team with limited direction from the production supervisor.
Works with Engineering to develop new processes, provides feedback for the creation of new documentation (i.e. MPI, SOP), and trains others to these documents (as needed)
Consistently identifies improvements opportunities for tooling/fixtures.
Recommends and initiates actions to prevent the occurrence of product non-conformity and assists in the implementation and verification of solutions.
Must have good verbal and written communication skills.
Must be able to work with clear communication with cross functional teams and Engineers.
Demonstrates the ability to communicate with others via emails, written correspondence, ect.
Must have the ability to develop and encourage group communication and process improvement meetings. Facilitates with the implementation of process improvement (Kaizen) and Lean manufacturing activities. Provides feedback or ideas on process improvement i.e., bottleneck areas observed.
Has good understanding of Lean and 5s principles. Help enforce, follows, and adheres to the standards. Help lead groups in performing 5s audits.
Qualifications:
High school diploma or equivalent and 4+ years’ experience in the medical device/pharmaceutical field or in a related area
Must be able to work in a Controlled Environment
Must have good hand‐eye coordination.
Must have a good verbal and written communication skills.
Must be able to work with and clearly communicate with cross functional teams and engineers.
Demonstrates reading, writing and math skills comprehension.
Must be detail oriented and demonstrate a high level of inventory control skills (with respect to accuracy and counts)
Must be able to accurately verify others’ work for accuracy (i.e. work content, actual part counts, LHR documentation)
Must be able to work cross-functional groups to resolve any discrepancies/documentation errors.
Must have intermediate to advanced computer skills (i.e. Microsoft Excel, Word, Outlook)
Reference: 200022738
https://jobs.careeraddict.com/post/95934957
Lead Operator - Prod Ops (Second Shift)
Posted on Oct 7, 2024 by Cordis
Santa Clara, CA
Other
Immediate Start
Annual Salary
Full-Time
Overview:
About Us:
Cordis is an independent, customer-focused global provider of interventional cardiovascular medical technologies. During our 60+ year history we’ve established a legacy of pioneering breakthrough technologies, including the first guiding catheters and coronary drug eluting stents. Cordis has built a strong global footprint that spans over 70 countries.
We’re teammates, not just employees. Our culture empowers you to act like an owner and unleash your full potential in the process. With diverse teams on a global scale, we foster an inclusive atmosphere where everyone is embraced for who they are, their unique perspective, and what they bring to the table. We believe the richness of our experiences and backgrounds enhances the careers of our teammates, the service to our customers, and ultimately, the lives of our patients.
If you love a challenge and are ready to have a direct, positive impact on the lives of millions, then Cordis is just the place for you. Join us, and let’s improve the wellbeing of millions, together.
We are the people behind the people who keep saving lives.
The 2nd shift Lead Operator, Production Ops builds product by following all Quality Systems and Processes (in which trained and certified to) and complete other assigned tasks while meeting manufacturing goals and metrics.
Responsibilities:
Adheres to all Quality Policies and Systems of the Company.
Maintains accurate records, including Lot History Records (LHR), and adheres to all GMP/GDP Policies.
Must be able to manage 20+ team members in work area.
Must be able to create work schedules based on production build schedule.
Must be able to process small parts under a microscope.
Frequently exceeds the average cycle time and quality standard requirements for the stations/processes trained/certified to.
Maintains an good level of attendance (including scheduled overtime)
Trains and possesses a detailed understanding of all processes in their area of responsibility.
Responsible and accountable to train teammates or other manufacturing support (I.e., MEs, QA, R&D, and ect.)
Flexes and rotates to other stations as necessary or assigned.
Maintains a professional work relationship with other team members and other cross‐functional groups.
Proficient in a wide variety of operations; can function as a subject matter expert (SME) for the area to help train and/or identify process improvements.
Helps to ensure that the teams are consistently maintaining accurate records.
Serves as a role model for ensuring Quality System Regulations adherence.
Analyses production metrics to suggest improvements for inefficiencies on the production floor and maximizes production output while ensuring high product quality.
Understands and follows safety policies and practices, and escalates any issues related to product, Quality or workplace safety.
Follows and adheres to 5S principles and goals.
Effectively fills in for the supervisor when not available; in this role, responsible training others, managing the production floor activities as needed, performing LHR reviews, performing limited troubleshooting activities, and notifying engineering/maintenance of issues.
Coordinates all Engineering Build Request (EBR) and Rework activities (training, execution of EBR, and documentation review. Provide feedback during validation and verification builds.
Encourages team to meet desired production metrics/goals while maintaining quality standards.
Advises the team with limited direction from the production supervisor.
Works with Engineering to develop new processes, provides feedback for the creation of new documentation (i.e. MPI, SOP), and trains others to these documents (as needed)
Consistently identifies improvements opportunities for tooling/fixtures.
Recommends and initiates actions to prevent the occurrence of product non-conformity and assists in the implementation and verification of solutions.
Must have good verbal and written communication skills.
Must be able to work with clear communication with cross functional teams and Engineers.
Demonstrates the ability to communicate with others via emails, written correspondence, ect.
Must have the ability to develop and encourage group communication and process improvement meetings. Facilitates with the implementation of process improvement (Kaizen) and Lean manufacturing activities. Provides feedback or ideas on process improvement i.e., bottleneck areas observed.
Has good understanding of Lean and 5s principles. Help enforce, follows, and adheres to the standards. Help lead groups in performing 5s audits.
Qualifications:
High school diploma or equivalent and 4+ years’ experience in the medical device/pharmaceutical field or in a related area
Must be able to work in a Controlled Environment
Must have good hand‐eye coordination.
Must have a good verbal and written communication skills.
Must be able to work with and clearly communicate with cross functional teams and engineers.
Demonstrates reading, writing and math skills comprehension.
Must be detail oriented and demonstrate a high level of inventory control skills (with respect to accuracy and counts)
Must be able to accurately verify others’ work for accuracy (i.e. work content, actual part counts, LHR documentation)
Must be able to work cross-functional groups to resolve any discrepancies/documentation errors.
Must have intermediate to advanced computer skills (i.e. Microsoft Excel, Word, Outlook)
About Us:
Cordis is an independent, customer-focused global provider of interventional cardiovascular medical technologies. During our 60+ year history we’ve established a legacy of pioneering breakthrough technologies, including the first guiding catheters and coronary drug eluting stents. Cordis has built a strong global footprint that spans over 70 countries.
We’re teammates, not just employees. Our culture empowers you to act like an owner and unleash your full potential in the process. With diverse teams on a global scale, we foster an inclusive atmosphere where everyone is embraced for who they are, their unique perspective, and what they bring to the table. We believe the richness of our experiences and backgrounds enhances the careers of our teammates, the service to our customers, and ultimately, the lives of our patients.
If you love a challenge and are ready to have a direct, positive impact on the lives of millions, then Cordis is just the place for you. Join us, and let’s improve the wellbeing of millions, together.
We are the people behind the people who keep saving lives.
The 2nd shift Lead Operator, Production Ops builds product by following all Quality Systems and Processes (in which trained and certified to) and complete other assigned tasks while meeting manufacturing goals and metrics.
Responsibilities:
Adheres to all Quality Policies and Systems of the Company.
Maintains accurate records, including Lot History Records (LHR), and adheres to all GMP/GDP Policies.
Must be able to manage 20+ team members in work area.
Must be able to create work schedules based on production build schedule.
Must be able to process small parts under a microscope.
Frequently exceeds the average cycle time and quality standard requirements for the stations/processes trained/certified to.
Maintains an good level of attendance (including scheduled overtime)
Trains and possesses a detailed understanding of all processes in their area of responsibility.
Responsible and accountable to train teammates or other manufacturing support (I.e., MEs, QA, R&D, and ect.)
Flexes and rotates to other stations as necessary or assigned.
Maintains a professional work relationship with other team members and other cross‐functional groups.
Proficient in a wide variety of operations; can function as a subject matter expert (SME) for the area to help train and/or identify process improvements.
Helps to ensure that the teams are consistently maintaining accurate records.
Serves as a role model for ensuring Quality System Regulations adherence.
Analyses production metrics to suggest improvements for inefficiencies on the production floor and maximizes production output while ensuring high product quality.
Understands and follows safety policies and practices, and escalates any issues related to product, Quality or workplace safety.
Follows and adheres to 5S principles and goals.
Effectively fills in for the supervisor when not available; in this role, responsible training others, managing the production floor activities as needed, performing LHR reviews, performing limited troubleshooting activities, and notifying engineering/maintenance of issues.
Coordinates all Engineering Build Request (EBR) and Rework activities (training, execution of EBR, and documentation review. Provide feedback during validation and verification builds.
Encourages team to meet desired production metrics/goals while maintaining quality standards.
Advises the team with limited direction from the production supervisor.
Works with Engineering to develop new processes, provides feedback for the creation of new documentation (i.e. MPI, SOP), and trains others to these documents (as needed)
Consistently identifies improvements opportunities for tooling/fixtures.
Recommends and initiates actions to prevent the occurrence of product non-conformity and assists in the implementation and verification of solutions.
Must have good verbal and written communication skills.
Must be able to work with clear communication with cross functional teams and Engineers.
Demonstrates the ability to communicate with others via emails, written correspondence, ect.
Must have the ability to develop and encourage group communication and process improvement meetings. Facilitates with the implementation of process improvement (Kaizen) and Lean manufacturing activities. Provides feedback or ideas on process improvement i.e., bottleneck areas observed.
Has good understanding of Lean and 5s principles. Help enforce, follows, and adheres to the standards. Help lead groups in performing 5s audits.
Qualifications:
High school diploma or equivalent and 4+ years’ experience in the medical device/pharmaceutical field or in a related area
Must be able to work in a Controlled Environment
Must have good hand‐eye coordination.
Must have a good verbal and written communication skills.
Must be able to work with and clearly communicate with cross functional teams and engineers.
Demonstrates reading, writing and math skills comprehension.
Must be detail oriented and demonstrate a high level of inventory control skills (with respect to accuracy and counts)
Must be able to accurately verify others’ work for accuracy (i.e. work content, actual part counts, LHR documentation)
Must be able to work cross-functional groups to resolve any discrepancies/documentation errors.
Must have intermediate to advanced computer skills (i.e. Microsoft Excel, Word, Outlook)
Reference: 200022738
Share this job:
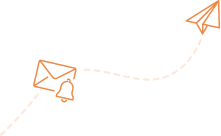
Alert me to jobs like this:
Amplify your job search:
Expert career advice
Increase interview chances with our downloads and specialist services.
Visit Blog