Precast Concrete Plant Manager
Posted on Sep 21, 2024 by Enterprise Precast Concrete
Kansas City, KS
Admin & Secretarial
Immediate Start
Annual Salary
Full-Time
General Summary of Responsibilities:
This position directs all production and production-related activity from ordering and receiving of raw materials to the storage of the finished product in the yard; directs and coaches the individuals who head up Production, Carpenter Shop, Steel Shop, Finish and Yard Operations, and Maintenance; communicates and collaborates with these foremen and Quality Control personnel to optimize production quality and workflow; and assists the General Manager in interpreting and administering company policy and procedures.
Essential Duties and Job Responsibilities:
1. Works with the Operations Manager to provide information to estimators related to establishment of general guidelines for precast panel costs, and provides input to estimators regarding specific jobs, related to degree of production difficulty or opportunities for innovation.
2. Establishes and manages production schedules and table utilization.
3. Conducts daily production meetings to discuss production schedules, concerns, and opportunities for improvement, and to ensure ongoing organizational teamwork.
4. Directs the production of precast products to ensure that architectural specifications and PCI/NPCA/ACPA/AAR M1003 requirements are consistently met or exceeded, including fabrication of forms, determination of mix designs, preparation of samples, construction and stripping of precast products, and finishing and yarding.
5. Attends weekly staff meetings to keep informed on the status of each project, potential schedule changes, change orders, shipping requirements, and other project requirements; as well as to collaborate with other managers on project-related issues.
6. Collaborates with the Operations Manager regarding sample submittal, project status, and production scheduling and fabrication, with an emphasis on customer-focused organizational teamwork and mutual respect.
7. Works with the Steel Shop Coordinator to ensure that all steel items are on hand and assembled in a manner that optimizes production.
8. Works with the Finish Foreman and Traffic Manager to ensure that finished products are stored in an efficient and accessible manner, utilizing erection sequences as a resource whenever possible.
9. Evaluates the work of directly reporting individuals for the purpose of determining skill level, training needs, and potential for increased responsibility; and serves as a coach to help these employees expand their career opportunities
10. Works with the Maintenance Mechanic to ensure that repair and maintenance activities are carried out in a cost-effective and timely manner.
11. Ensures that good housekeeping is maintained in the plant.
12. Establishes and manages a process that ensures follow up on repairs and rework, both by accomplishing the required work and by determining and addressing the underlying cause of poor quality.
13. Collaborates with Quality Control personnel to ensure that production is done in accordance with QC requirements.
14. Assumes responsibility for ordering all chemicals, cement, aggregate, lumber, rebar, steel shop inventory items, and other supplies and materials related to production.
15. Serves as a role model for employees with regard to attendance, timeliness, loyalty, mutual respect and support for organizational teamwork and continuous process improvement.
16. Conducts performance appraisals of those employees who are direct reports, and reviews recommended salary or status adjustments with the General Manager. Reviews with plant foremen the preliminary performance appraisals which they have conducted with their own people.
17. Monitors actual production labor costs per panel versus the labor costs established in the bid, and engages production personnel in problem-solving if a negative trend is identified.
18. Works with the plant foremen to track and reduce the level of precast panel rework and fixes.
Requirements
Education and Experience
Four-year college degree in engineering or a related fields and a minimum of five years of related experience in the precast industry.
Language Skills
Ability to read, analyze and interpret general business periodicals, technical procedures, technical specifications, cost analyses and governmental regulations. Ability to effectively write procedures, business correspondence and technical reports. Ability to effectively present ideas and information to employees, managers, customers and vendors. Ability to read and understand construction documents for building projects.
Technical/Mathematical Skills
Ability to apply concepts of mathematics to the work environment, to develop and utilize statistical information, and to perform cost/benefit analyses related to potential process and equipment changes. Ability to understand, utilize and enhance personal computer and network software and hardware applicable to the company’s operations, including word processing, spreadsheets, database software, electronic mail, and graphics.
Reasoning Ability
Ability to define problems, collect data, establish facts, draw valid conclusions and develop logical and innovative solutions. Ability to interpret a variety of technical instructions in mathematical or diagram form.
Physical Demands
The physical demands described here are representative of those that must be meet by an employee to successfully perform the essential functions of this job. Reasonable accommodations may be made to enable individuals with disabilities to perform the essential functions.
While performing the duties of this job, the employee is regularly required to walk, climb, sit, use hands to finger, handle or feel objects, tools or controls; and talk and hear. Manual lifting requirements are moderate to heavy, but with the assistance of other personnel and cranes.
Work Environment
The work environment characteristics described her are representative of those the employee encounters while performing the essential duties and responsibilities of the job. The work described will require the Plant Manager to be in the plant a majority of the time. This employee will be required to wear all safety equipment required of regular plant personnel, and may be exposed to fumes and airborne particles. The employee may be exposed to toxic or caustic chemicals, but will be provided with protective equipment. The noise level is low, with occasional periods of moderate noise.
Enterprise Precast Concrete is a member of the Enterprise Properties family of companies.
Pre-Employment Drug Screen, Post Offer Physical, Criminal Background Check & Employment Verification are all part of our hiring process.
Benefits
Medical, Dental & Vision
Competitive Compensation
Profit Sharing
401k with Match
This position directs all production and production-related activity from ordering and receiving of raw materials to the storage of the finished product in the yard; directs and coaches the individuals who head up Production, Carpenter Shop, Steel Shop, Finish and Yard Operations, and Maintenance; communicates and collaborates with these foremen and Quality Control personnel to optimize production quality and workflow; and assists the General Manager in interpreting and administering company policy and procedures.
Essential Duties and Job Responsibilities:
1. Works with the Operations Manager to provide information to estimators related to establishment of general guidelines for precast panel costs, and provides input to estimators regarding specific jobs, related to degree of production difficulty or opportunities for innovation.
2. Establishes and manages production schedules and table utilization.
3. Conducts daily production meetings to discuss production schedules, concerns, and opportunities for improvement, and to ensure ongoing organizational teamwork.
4. Directs the production of precast products to ensure that architectural specifications and PCI/NPCA/ACPA/AAR M1003 requirements are consistently met or exceeded, including fabrication of forms, determination of mix designs, preparation of samples, construction and stripping of precast products, and finishing and yarding.
5. Attends weekly staff meetings to keep informed on the status of each project, potential schedule changes, change orders, shipping requirements, and other project requirements; as well as to collaborate with other managers on project-related issues.
6. Collaborates with the Operations Manager regarding sample submittal, project status, and production scheduling and fabrication, with an emphasis on customer-focused organizational teamwork and mutual respect.
7. Works with the Steel Shop Coordinator to ensure that all steel items are on hand and assembled in a manner that optimizes production.
8. Works with the Finish Foreman and Traffic Manager to ensure that finished products are stored in an efficient and accessible manner, utilizing erection sequences as a resource whenever possible.
9. Evaluates the work of directly reporting individuals for the purpose of determining skill level, training needs, and potential for increased responsibility; and serves as a coach to help these employees expand their career opportunities
10. Works with the Maintenance Mechanic to ensure that repair and maintenance activities are carried out in a cost-effective and timely manner.
11. Ensures that good housekeeping is maintained in the plant.
12. Establishes and manages a process that ensures follow up on repairs and rework, both by accomplishing the required work and by determining and addressing the underlying cause of poor quality.
13. Collaborates with Quality Control personnel to ensure that production is done in accordance with QC requirements.
14. Assumes responsibility for ordering all chemicals, cement, aggregate, lumber, rebar, steel shop inventory items, and other supplies and materials related to production.
15. Serves as a role model for employees with regard to attendance, timeliness, loyalty, mutual respect and support for organizational teamwork and continuous process improvement.
16. Conducts performance appraisals of those employees who are direct reports, and reviews recommended salary or status adjustments with the General Manager. Reviews with plant foremen the preliminary performance appraisals which they have conducted with their own people.
17. Monitors actual production labor costs per panel versus the labor costs established in the bid, and engages production personnel in problem-solving if a negative trend is identified.
18. Works with the plant foremen to track and reduce the level of precast panel rework and fixes.
Requirements
Education and Experience
Four-year college degree in engineering or a related fields and a minimum of five years of related experience in the precast industry.
Language Skills
Ability to read, analyze and interpret general business periodicals, technical procedures, technical specifications, cost analyses and governmental regulations. Ability to effectively write procedures, business correspondence and technical reports. Ability to effectively present ideas and information to employees, managers, customers and vendors. Ability to read and understand construction documents for building projects.
Technical/Mathematical Skills
Ability to apply concepts of mathematics to the work environment, to develop and utilize statistical information, and to perform cost/benefit analyses related to potential process and equipment changes. Ability to understand, utilize and enhance personal computer and network software and hardware applicable to the company’s operations, including word processing, spreadsheets, database software, electronic mail, and graphics.
Reasoning Ability
Ability to define problems, collect data, establish facts, draw valid conclusions and develop logical and innovative solutions. Ability to interpret a variety of technical instructions in mathematical or diagram form.
Physical Demands
The physical demands described here are representative of those that must be meet by an employee to successfully perform the essential functions of this job. Reasonable accommodations may be made to enable individuals with disabilities to perform the essential functions.
While performing the duties of this job, the employee is regularly required to walk, climb, sit, use hands to finger, handle or feel objects, tools or controls; and talk and hear. Manual lifting requirements are moderate to heavy, but with the assistance of other personnel and cranes.
Work Environment
The work environment characteristics described her are representative of those the employee encounters while performing the essential duties and responsibilities of the job. The work described will require the Plant Manager to be in the plant a majority of the time. This employee will be required to wear all safety equipment required of regular plant personnel, and may be exposed to fumes and airborne particles. The employee may be exposed to toxic or caustic chemicals, but will be provided with protective equipment. The noise level is low, with occasional periods of moderate noise.
Enterprise Precast Concrete is a member of the Enterprise Properties family of companies.
Pre-Employment Drug Screen, Post Offer Physical, Criminal Background Check & Employment Verification are all part of our hiring process.
Benefits
Medical, Dental & Vision
Competitive Compensation
Profit Sharing
401k with Match
Reference: 202106656
https://jobs.careeraddict.com/post/95494175
Precast Concrete Plant Manager
Posted on Sep 21, 2024 by Enterprise Precast Concrete
Kansas City, KS
Admin & Secretarial
Immediate Start
Annual Salary
Full-Time
General Summary of Responsibilities:
This position directs all production and production-related activity from ordering and receiving of raw materials to the storage of the finished product in the yard; directs and coaches the individuals who head up Production, Carpenter Shop, Steel Shop, Finish and Yard Operations, and Maintenance; communicates and collaborates with these foremen and Quality Control personnel to optimize production quality and workflow; and assists the General Manager in interpreting and administering company policy and procedures.
Essential Duties and Job Responsibilities:
1. Works with the Operations Manager to provide information to estimators related to establishment of general guidelines for precast panel costs, and provides input to estimators regarding specific jobs, related to degree of production difficulty or opportunities for innovation.
2. Establishes and manages production schedules and table utilization.
3. Conducts daily production meetings to discuss production schedules, concerns, and opportunities for improvement, and to ensure ongoing organizational teamwork.
4. Directs the production of precast products to ensure that architectural specifications and PCI/NPCA/ACPA/AAR M1003 requirements are consistently met or exceeded, including fabrication of forms, determination of mix designs, preparation of samples, construction and stripping of precast products, and finishing and yarding.
5. Attends weekly staff meetings to keep informed on the status of each project, potential schedule changes, change orders, shipping requirements, and other project requirements; as well as to collaborate with other managers on project-related issues.
6. Collaborates with the Operations Manager regarding sample submittal, project status, and production scheduling and fabrication, with an emphasis on customer-focused organizational teamwork and mutual respect.
7. Works with the Steel Shop Coordinator to ensure that all steel items are on hand and assembled in a manner that optimizes production.
8. Works with the Finish Foreman and Traffic Manager to ensure that finished products are stored in an efficient and accessible manner, utilizing erection sequences as a resource whenever possible.
9. Evaluates the work of directly reporting individuals for the purpose of determining skill level, training needs, and potential for increased responsibility; and serves as a coach to help these employees expand their career opportunities
10. Works with the Maintenance Mechanic to ensure that repair and maintenance activities are carried out in a cost-effective and timely manner.
11. Ensures that good housekeeping is maintained in the plant.
12. Establishes and manages a process that ensures follow up on repairs and rework, both by accomplishing the required work and by determining and addressing the underlying cause of poor quality.
13. Collaborates with Quality Control personnel to ensure that production is done in accordance with QC requirements.
14. Assumes responsibility for ordering all chemicals, cement, aggregate, lumber, rebar, steel shop inventory items, and other supplies and materials related to production.
15. Serves as a role model for employees with regard to attendance, timeliness, loyalty, mutual respect and support for organizational teamwork and continuous process improvement.
16. Conducts performance appraisals of those employees who are direct reports, and reviews recommended salary or status adjustments with the General Manager. Reviews with plant foremen the preliminary performance appraisals which they have conducted with their own people.
17. Monitors actual production labor costs per panel versus the labor costs established in the bid, and engages production personnel in problem-solving if a negative trend is identified.
18. Works with the plant foremen to track and reduce the level of precast panel rework and fixes.
Requirements
Education and Experience
Four-year college degree in engineering or a related fields and a minimum of five years of related experience in the precast industry.
Language Skills
Ability to read, analyze and interpret general business periodicals, technical procedures, technical specifications, cost analyses and governmental regulations. Ability to effectively write procedures, business correspondence and technical reports. Ability to effectively present ideas and information to employees, managers, customers and vendors. Ability to read and understand construction documents for building projects.
Technical/Mathematical Skills
Ability to apply concepts of mathematics to the work environment, to develop and utilize statistical information, and to perform cost/benefit analyses related to potential process and equipment changes. Ability to understand, utilize and enhance personal computer and network software and hardware applicable to the company’s operations, including word processing, spreadsheets, database software, electronic mail, and graphics.
Reasoning Ability
Ability to define problems, collect data, establish facts, draw valid conclusions and develop logical and innovative solutions. Ability to interpret a variety of technical instructions in mathematical or diagram form.
Physical Demands
The physical demands described here are representative of those that must be meet by an employee to successfully perform the essential functions of this job. Reasonable accommodations may be made to enable individuals with disabilities to perform the essential functions.
While performing the duties of this job, the employee is regularly required to walk, climb, sit, use hands to finger, handle or feel objects, tools or controls; and talk and hear. Manual lifting requirements are moderate to heavy, but with the assistance of other personnel and cranes.
Work Environment
The work environment characteristics described her are representative of those the employee encounters while performing the essential duties and responsibilities of the job. The work described will require the Plant Manager to be in the plant a majority of the time. This employee will be required to wear all safety equipment required of regular plant personnel, and may be exposed to fumes and airborne particles. The employee may be exposed to toxic or caustic chemicals, but will be provided with protective equipment. The noise level is low, with occasional periods of moderate noise.
Enterprise Precast Concrete is a member of the Enterprise Properties family of companies.
Pre-Employment Drug Screen, Post Offer Physical, Criminal Background Check & Employment Verification are all part of our hiring process.
Benefits
Medical, Dental & Vision
Competitive Compensation
Profit Sharing
401k with Match
This position directs all production and production-related activity from ordering and receiving of raw materials to the storage of the finished product in the yard; directs and coaches the individuals who head up Production, Carpenter Shop, Steel Shop, Finish and Yard Operations, and Maintenance; communicates and collaborates with these foremen and Quality Control personnel to optimize production quality and workflow; and assists the General Manager in interpreting and administering company policy and procedures.
Essential Duties and Job Responsibilities:
1. Works with the Operations Manager to provide information to estimators related to establishment of general guidelines for precast panel costs, and provides input to estimators regarding specific jobs, related to degree of production difficulty or opportunities for innovation.
2. Establishes and manages production schedules and table utilization.
3. Conducts daily production meetings to discuss production schedules, concerns, and opportunities for improvement, and to ensure ongoing organizational teamwork.
4. Directs the production of precast products to ensure that architectural specifications and PCI/NPCA/ACPA/AAR M1003 requirements are consistently met or exceeded, including fabrication of forms, determination of mix designs, preparation of samples, construction and stripping of precast products, and finishing and yarding.
5. Attends weekly staff meetings to keep informed on the status of each project, potential schedule changes, change orders, shipping requirements, and other project requirements; as well as to collaborate with other managers on project-related issues.
6. Collaborates with the Operations Manager regarding sample submittal, project status, and production scheduling and fabrication, with an emphasis on customer-focused organizational teamwork and mutual respect.
7. Works with the Steel Shop Coordinator to ensure that all steel items are on hand and assembled in a manner that optimizes production.
8. Works with the Finish Foreman and Traffic Manager to ensure that finished products are stored in an efficient and accessible manner, utilizing erection sequences as a resource whenever possible.
9. Evaluates the work of directly reporting individuals for the purpose of determining skill level, training needs, and potential for increased responsibility; and serves as a coach to help these employees expand their career opportunities
10. Works with the Maintenance Mechanic to ensure that repair and maintenance activities are carried out in a cost-effective and timely manner.
11. Ensures that good housekeeping is maintained in the plant.
12. Establishes and manages a process that ensures follow up on repairs and rework, both by accomplishing the required work and by determining and addressing the underlying cause of poor quality.
13. Collaborates with Quality Control personnel to ensure that production is done in accordance with QC requirements.
14. Assumes responsibility for ordering all chemicals, cement, aggregate, lumber, rebar, steel shop inventory items, and other supplies and materials related to production.
15. Serves as a role model for employees with regard to attendance, timeliness, loyalty, mutual respect and support for organizational teamwork and continuous process improvement.
16. Conducts performance appraisals of those employees who are direct reports, and reviews recommended salary or status adjustments with the General Manager. Reviews with plant foremen the preliminary performance appraisals which they have conducted with their own people.
17. Monitors actual production labor costs per panel versus the labor costs established in the bid, and engages production personnel in problem-solving if a negative trend is identified.
18. Works with the plant foremen to track and reduce the level of precast panel rework and fixes.
Requirements
Education and Experience
Four-year college degree in engineering or a related fields and a minimum of five years of related experience in the precast industry.
Language Skills
Ability to read, analyze and interpret general business periodicals, technical procedures, technical specifications, cost analyses and governmental regulations. Ability to effectively write procedures, business correspondence and technical reports. Ability to effectively present ideas and information to employees, managers, customers and vendors. Ability to read and understand construction documents for building projects.
Technical/Mathematical Skills
Ability to apply concepts of mathematics to the work environment, to develop and utilize statistical information, and to perform cost/benefit analyses related to potential process and equipment changes. Ability to understand, utilize and enhance personal computer and network software and hardware applicable to the company’s operations, including word processing, spreadsheets, database software, electronic mail, and graphics.
Reasoning Ability
Ability to define problems, collect data, establish facts, draw valid conclusions and develop logical and innovative solutions. Ability to interpret a variety of technical instructions in mathematical or diagram form.
Physical Demands
The physical demands described here are representative of those that must be meet by an employee to successfully perform the essential functions of this job. Reasonable accommodations may be made to enable individuals with disabilities to perform the essential functions.
While performing the duties of this job, the employee is regularly required to walk, climb, sit, use hands to finger, handle or feel objects, tools or controls; and talk and hear. Manual lifting requirements are moderate to heavy, but with the assistance of other personnel and cranes.
Work Environment
The work environment characteristics described her are representative of those the employee encounters while performing the essential duties and responsibilities of the job. The work described will require the Plant Manager to be in the plant a majority of the time. This employee will be required to wear all safety equipment required of regular plant personnel, and may be exposed to fumes and airborne particles. The employee may be exposed to toxic or caustic chemicals, but will be provided with protective equipment. The noise level is low, with occasional periods of moderate noise.
Enterprise Precast Concrete is a member of the Enterprise Properties family of companies.
Pre-Employment Drug Screen, Post Offer Physical, Criminal Background Check & Employment Verification are all part of our hiring process.
Benefits
Medical, Dental & Vision
Competitive Compensation
Profit Sharing
401k with Match
Reference: 202106656
Share this job:
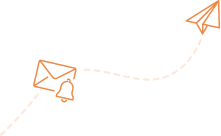
Alert me to jobs like this:
Amplify your job search:
Expert career advice
Increase interview chances with our downloads and specialist services.
Visit Blog