Quality and Continuous Improvement Manager
Posted on Sep 17, 2024 by Real Alloy
Wabash, IN
Admin & Secretarial
Immediate Start
Annual Salary
Full-Time
Overview:
REAL ALLOY is the market leader in third-party aluminum recycling and specification alloy production. Headquartered in Cleveland, Ohio, we have 17 plants strategically located across the United States, Mexico, and Canada. We convert aluminum scrap and by-products into reusable aluminum metal for a growing number of applications across various industries. We are ideally positioned to respond to the needs of an increasingly recycling-conscious world. Advanced technologies enable us to process a large variety of scrap and dross and reduce the amount of residual waste from aluminum manufacturing that would otherwise end up as landfill.
Responsibilities:
Real Alloy is seeking a qualified individual who will provide leadership to the ISO based Continuous Improvement. Promote Best Operating practices, engage in operational improvement projects, and assist with customer related issues. Candidate will execute lean transformation as well as facilitate kaizen events in all plant areas.
Train and develop plant leaders on lean principles, cultural transformation, and the lean leader mindset.
Provide lean methodology expertise for plant wide ROS deployment, including core tools: 5S, MDI, A3 Thinking, Standardized Work, VSM, TPM, and Problem Solving while spending 40% of working time on the plant floor identifying, correcting, and controlling waste.
Drive change with business leadership team to enable Real Alloy to continuously improve performance, which includes managing the transformation roadmap, and leveraging Information Centers for continuous improvement, and creating a visual workplace.
Recommend or implement, approved, cost reduction and/or efficiency improvement initiatives. Prioritize based on ROI, track improvements and report via metrics.
Providing event follow-up to monitor the progress of planned improvement implementation to assure timely action, appropriate management support, and achievement of expected tangible benefits.
Using appropriate measurement, analysis and evaluation methods to accurately identify and document process improvements financially.
Quantify material blending effectiveness and relate to financial performance.
Develop and complete a plan designed to improve the skills and knowledge necessary to this position. Keep current regarding new innovations and recommend new procedures to reduce costs.
Qualifications:
Bachelor’s degree, preferably in Engineering, Manufacturing/Operations, or an equivalent level of degree.
3-5 years’ experience in Process Engineering
3-5 years’ experience in Lean Six Sigma
1 + years’ experience facilitating kaizen events and lean transformations.
Proven ability to successfully manage cross functional teams, and implement improvement within an established time frame, then sustain process improvements
Excellent interpersonal, written, and verbal communication and organizational skills. Must be able to prepare and deliver presentations regarding project results.
High energy, data driven, and results oriented.
Willingness to travel approximately 10% of the time, if needed.
Preferred:
Masters in Engineering preferred.
Experience managing ISO 9000 or TS16949 Quality Management Systems preferred.
DMAIC/Black or Green Belt problem solving skills a plus
Working knowledge of aluminum processes is a plus.
:
The above statements are intended to describe the general nature and level of work performed by people assigned to this classification. They are not construed to be an exhaustive list of all job duties performed by the personnel so classified.
Equal Opportunity:
REAL ALLOY is an equal opportunity employer and supports diversity in the workplace. Qualified applications will receive consideration for employment without regard to their race, color, religion, sex, sexual orientation, gender identity, national origin, disability, or status as a protected veteran. Our HR teams will reach out to the applicants who met the qualifications and most closely aligned with requirements of the positions.
REAL ALLOY is the market leader in third-party aluminum recycling and specification alloy production. Headquartered in Cleveland, Ohio, we have 17 plants strategically located across the United States, Mexico, and Canada. We convert aluminum scrap and by-products into reusable aluminum metal for a growing number of applications across various industries. We are ideally positioned to respond to the needs of an increasingly recycling-conscious world. Advanced technologies enable us to process a large variety of scrap and dross and reduce the amount of residual waste from aluminum manufacturing that would otherwise end up as landfill.
Responsibilities:
Real Alloy is seeking a qualified individual who will provide leadership to the ISO based Continuous Improvement. Promote Best Operating practices, engage in operational improvement projects, and assist with customer related issues. Candidate will execute lean transformation as well as facilitate kaizen events in all plant areas.
Train and develop plant leaders on lean principles, cultural transformation, and the lean leader mindset.
Provide lean methodology expertise for plant wide ROS deployment, including core tools: 5S, MDI, A3 Thinking, Standardized Work, VSM, TPM, and Problem Solving while spending 40% of working time on the plant floor identifying, correcting, and controlling waste.
Drive change with business leadership team to enable Real Alloy to continuously improve performance, which includes managing the transformation roadmap, and leveraging Information Centers for continuous improvement, and creating a visual workplace.
Recommend or implement, approved, cost reduction and/or efficiency improvement initiatives. Prioritize based on ROI, track improvements and report via metrics.
Providing event follow-up to monitor the progress of planned improvement implementation to assure timely action, appropriate management support, and achievement of expected tangible benefits.
Using appropriate measurement, analysis and evaluation methods to accurately identify and document process improvements financially.
Quantify material blending effectiveness and relate to financial performance.
Develop and complete a plan designed to improve the skills and knowledge necessary to this position. Keep current regarding new innovations and recommend new procedures to reduce costs.
Qualifications:
Bachelor’s degree, preferably in Engineering, Manufacturing/Operations, or an equivalent level of degree.
3-5 years’ experience in Process Engineering
3-5 years’ experience in Lean Six Sigma
1 + years’ experience facilitating kaizen events and lean transformations.
Proven ability to successfully manage cross functional teams, and implement improvement within an established time frame, then sustain process improvements
Excellent interpersonal, written, and verbal communication and organizational skills. Must be able to prepare and deliver presentations regarding project results.
High energy, data driven, and results oriented.
Willingness to travel approximately 10% of the time, if needed.
Preferred:
Masters in Engineering preferred.
Experience managing ISO 9000 or TS16949 Quality Management Systems preferred.
DMAIC/Black or Green Belt problem solving skills a plus
Working knowledge of aluminum processes is a plus.
:
The above statements are intended to describe the general nature and level of work performed by people assigned to this classification. They are not construed to be an exhaustive list of all job duties performed by the personnel so classified.
Equal Opportunity:
REAL ALLOY is an equal opportunity employer and supports diversity in the workplace. Qualified applications will receive consideration for employment without regard to their race, color, religion, sex, sexual orientation, gender identity, national origin, disability, or status as a protected veteran. Our HR teams will reach out to the applicants who met the qualifications and most closely aligned with requirements of the positions.
Reference: 200949035
https://jobs.careeraddict.com/post/95379374
Quality and Continuous Improvement Manager
Posted on Sep 17, 2024 by Real Alloy
Wabash, IN
Admin & Secretarial
Immediate Start
Annual Salary
Full-Time
Overview:
REAL ALLOY is the market leader in third-party aluminum recycling and specification alloy production. Headquartered in Cleveland, Ohio, we have 17 plants strategically located across the United States, Mexico, and Canada. We convert aluminum scrap and by-products into reusable aluminum metal for a growing number of applications across various industries. We are ideally positioned to respond to the needs of an increasingly recycling-conscious world. Advanced technologies enable us to process a large variety of scrap and dross and reduce the amount of residual waste from aluminum manufacturing that would otherwise end up as landfill.
Responsibilities:
Real Alloy is seeking a qualified individual who will provide leadership to the ISO based Continuous Improvement. Promote Best Operating practices, engage in operational improvement projects, and assist with customer related issues. Candidate will execute lean transformation as well as facilitate kaizen events in all plant areas.
Train and develop plant leaders on lean principles, cultural transformation, and the lean leader mindset.
Provide lean methodology expertise for plant wide ROS deployment, including core tools: 5S, MDI, A3 Thinking, Standardized Work, VSM, TPM, and Problem Solving while spending 40% of working time on the plant floor identifying, correcting, and controlling waste.
Drive change with business leadership team to enable Real Alloy to continuously improve performance, which includes managing the transformation roadmap, and leveraging Information Centers for continuous improvement, and creating a visual workplace.
Recommend or implement, approved, cost reduction and/or efficiency improvement initiatives. Prioritize based on ROI, track improvements and report via metrics.
Providing event follow-up to monitor the progress of planned improvement implementation to assure timely action, appropriate management support, and achievement of expected tangible benefits.
Using appropriate measurement, analysis and evaluation methods to accurately identify and document process improvements financially.
Quantify material blending effectiveness and relate to financial performance.
Develop and complete a plan designed to improve the skills and knowledge necessary to this position. Keep current regarding new innovations and recommend new procedures to reduce costs.
Qualifications:
Bachelor’s degree, preferably in Engineering, Manufacturing/Operations, or an equivalent level of degree.
3-5 years’ experience in Process Engineering
3-5 years’ experience in Lean Six Sigma
1 + years’ experience facilitating kaizen events and lean transformations.
Proven ability to successfully manage cross functional teams, and implement improvement within an established time frame, then sustain process improvements
Excellent interpersonal, written, and verbal communication and organizational skills. Must be able to prepare and deliver presentations regarding project results.
High energy, data driven, and results oriented.
Willingness to travel approximately 10% of the time, if needed.
Preferred:
Masters in Engineering preferred.
Experience managing ISO 9000 or TS16949 Quality Management Systems preferred.
DMAIC/Black or Green Belt problem solving skills a plus
Working knowledge of aluminum processes is a plus.
:
The above statements are intended to describe the general nature and level of work performed by people assigned to this classification. They are not construed to be an exhaustive list of all job duties performed by the personnel so classified.
Equal Opportunity:
REAL ALLOY is an equal opportunity employer and supports diversity in the workplace. Qualified applications will receive consideration for employment without regard to their race, color, religion, sex, sexual orientation, gender identity, national origin, disability, or status as a protected veteran. Our HR teams will reach out to the applicants who met the qualifications and most closely aligned with requirements of the positions.
REAL ALLOY is the market leader in third-party aluminum recycling and specification alloy production. Headquartered in Cleveland, Ohio, we have 17 plants strategically located across the United States, Mexico, and Canada. We convert aluminum scrap and by-products into reusable aluminum metal for a growing number of applications across various industries. We are ideally positioned to respond to the needs of an increasingly recycling-conscious world. Advanced technologies enable us to process a large variety of scrap and dross and reduce the amount of residual waste from aluminum manufacturing that would otherwise end up as landfill.
Responsibilities:
Real Alloy is seeking a qualified individual who will provide leadership to the ISO based Continuous Improvement. Promote Best Operating practices, engage in operational improvement projects, and assist with customer related issues. Candidate will execute lean transformation as well as facilitate kaizen events in all plant areas.
Train and develop plant leaders on lean principles, cultural transformation, and the lean leader mindset.
Provide lean methodology expertise for plant wide ROS deployment, including core tools: 5S, MDI, A3 Thinking, Standardized Work, VSM, TPM, and Problem Solving while spending 40% of working time on the plant floor identifying, correcting, and controlling waste.
Drive change with business leadership team to enable Real Alloy to continuously improve performance, which includes managing the transformation roadmap, and leveraging Information Centers for continuous improvement, and creating a visual workplace.
Recommend or implement, approved, cost reduction and/or efficiency improvement initiatives. Prioritize based on ROI, track improvements and report via metrics.
Providing event follow-up to monitor the progress of planned improvement implementation to assure timely action, appropriate management support, and achievement of expected tangible benefits.
Using appropriate measurement, analysis and evaluation methods to accurately identify and document process improvements financially.
Quantify material blending effectiveness and relate to financial performance.
Develop and complete a plan designed to improve the skills and knowledge necessary to this position. Keep current regarding new innovations and recommend new procedures to reduce costs.
Qualifications:
Bachelor’s degree, preferably in Engineering, Manufacturing/Operations, or an equivalent level of degree.
3-5 years’ experience in Process Engineering
3-5 years’ experience in Lean Six Sigma
1 + years’ experience facilitating kaizen events and lean transformations.
Proven ability to successfully manage cross functional teams, and implement improvement within an established time frame, then sustain process improvements
Excellent interpersonal, written, and verbal communication and organizational skills. Must be able to prepare and deliver presentations regarding project results.
High energy, data driven, and results oriented.
Willingness to travel approximately 10% of the time, if needed.
Preferred:
Masters in Engineering preferred.
Experience managing ISO 9000 or TS16949 Quality Management Systems preferred.
DMAIC/Black or Green Belt problem solving skills a plus
Working knowledge of aluminum processes is a plus.
:
The above statements are intended to describe the general nature and level of work performed by people assigned to this classification. They are not construed to be an exhaustive list of all job duties performed by the personnel so classified.
Equal Opportunity:
REAL ALLOY is an equal opportunity employer and supports diversity in the workplace. Qualified applications will receive consideration for employment without regard to their race, color, religion, sex, sexual orientation, gender identity, national origin, disability, or status as a protected veteran. Our HR teams will reach out to the applicants who met the qualifications and most closely aligned with requirements of the positions.
Reference: 200949035
Share this job:
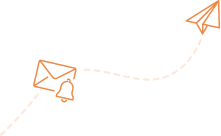
Alert me to jobs like this:
Amplify your job search:
Expert career advice
Increase interview chances with our downloads and specialist services.
Visit Blog